-
新闻资讯
- 激光应用
- 行业资讯
- 久恒风采
销售热线:17758118083
电话:0577-66871553
邮箱:sale@highlaser.cn
1688网店:https://laser2015.1688.com
总公司地址:浙江省瑞安市阁巷新区东二路138号32幢
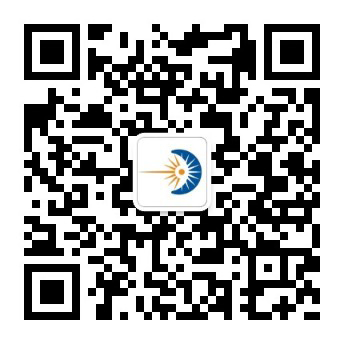
激光表面处理是采用大功率密度的激光束,以非接触性的方式加热材料表面.借助于材料表面本身传导冷却,来实现其表面改性的工艺技术。它在改善材料表面的力学性能和物理性能,以及提高零件的耐磨、耐蚀、耐疲劳性能方面大有裨益。近年来,激光清洗、激光淬火、激光合金化、激光冲击强化、激光退火等激光表面处理技术,以及激光熔覆和激光3D打印等激光增材制造技术迎来了广阔的应用前景。
激光表面处理及增材制造技术概述
当前,中国传统制造业正面临深度的转型升级,高附加值、高技术壁垒的高端精密加工是其中的重要方向之一,而激光表面处理便是核心精密加工技术,其优势显著:能量作用集中,热影响区小,工件变形小;能够处理表面形状复杂的工件,且容易实现自动化生产线。通过激光表面处理可以大幅改善工件制品的性能,提高其使用效能以及延长其使用寿命。
1. 激光清洗
激光清洗是近年来得到快速发展、应用广泛的一种新型表面清洁技术。它是采用高能脉冲激光束照射工件表面,使表面的污物、颗粒或涂层瞬间蒸发或膨胀剥离,从而达到洁净化的工艺过程。激光清洗主要分为除锈、除油、除漆、除涂层等工艺;主要应用于金属类清洗,文物类清洗,建筑类清洗等。基于其功能全面、加工精准灵活、高效节能、绿色环保、对基材无损伤、智能、清洗质量好、安全、应用范围广等特点和优势,它在各个工业领域愈发受青睐。
2. 激光淬火
激光淬火采用高能量激光作为热源,使金属表面快热快冷,瞬间完成淬火过程,得到高硬度、超细的马氏体组织,提高金属表面的硬度和耐磨性,并且在表面形成压应力,提高抗疲劳能力。这项工艺的核心优势包括热影响区小、变形量小、自动化程度高、选区淬火柔性好、细化晶粒硬度高和智能环保。譬如激光光斑可调,能够对任意宽度的位置进行淬火;其次,激光头配合多轴机器人联动,可对复杂零件的指定区域进行淬火。又如,激光淬火极热速冷,淬火应力及变形小。激光淬火前后工件的变形几乎可以忽略,因此特别适合高精度要求的零件表面处理。
当前,激光淬火已成功应用于汽车行业、模具行业、五金工具、机械行业行业中易损件的表面强化,尤其是在提高齿轮、轴面、导轨、钳口、模具等易损件的使用寿命方面,效果显著。
3. 激光合金化
激光合金化采用高能量激光作为热源,照射经过喷涂预制在金属工件表面的超细金属陶瓷材料,使之在激光束作用下快速熔凝渗透,从而改变工件表面的成分,获得组织细密、高耐磨的合金层,大幅提高工件在高温腐蚀条件下的耐磨性能。此项技术的成本低、无需后续加工 、变形小和速度快。
4. 激光冲击强化
激光冲击强化技术是利用强激光束产生的等离子冲击波,提高金属材料的抗疲劳、耐磨损和抗腐蚀能力的一种高新技术。它具有无热影响区、能量高效利用、超高应变率、可控性强以及强化效果显著等突出优点。同时,激光冲击强化具有更深的残余压应力、更好的微观组织和表面完整性、更好的热稳定性以及更长的寿命等特点。近年来该技术获得了迅速发展,在航空航天和国防军工等领域大有用武之地。另外,使用涂层的作用主要是保护工件不被激光灼伤并增强对激光能量的吸收,目前常用的涂层材料有黑漆和铝箔等。
5. 激光雕刻
激光雕刻加工是利用数控技术为基础,将高能量的激光束投射到材料表面,利用激光产生的热效应,在材料表面产生清晰图案的激光加工过程。加工材料在激光雕刻照射下瞬间的熔化和气化的物理变性,能使激光雕刻实现加工目的。激光雕刻就是运用激光在物件上面刻写文字,这种技术刻出来的字无刻痕,物体表面光滑平整,字迹亦不会磨损。其特点和优势涵盖:安全可靠;精确细致、精度可达到0.02mm;节约环保、加工节省材料;高速快捷、可根据输出的图样高速雕刻;成本低廉、不受加工数量限制等。
6. 激光退火
激光退火是指利用激光加热材料表面,将材料曝露于高温一段很长时间后,然后再慢慢冷却的热处理制程。该工艺主要目的是释放应力、增加材料延展性和韧性、产生特殊显微结构等。其特点是能够调整基体组织、降低硬度、细化晶粒和消除内应力。近年来,激光退火技术也成为半导体加工行业的一种新工艺,可大幅提高集成电路的集成度。
7. 激光熔覆
激光熔覆技术采用高能量激光作为热源,金属合金粉末作为焊材,通过激光与合金粉末同步作用于金属表面快速熔化形成熔池,再快速凝固形成致密、均匀并且厚度可控的冶金结合层,熔覆层具有特殊物理、化学或力学性能,从而达到修复工件表面尺寸、强化延长寿命的效果。近年来,它已成为国内外激光表面改性研究的热点。这一技术的特点和优势包括选材多样化、成型优异、平整光洁、冶金结合强度高和环保降耗等。
2020年12月,武钢华工激光公司联合苏州大学、华中科技大学申报的国家重点研发计划 “增材制造与激光制造”专项---“高效高精度多功能激光增材制造系列熔覆喷头研发”项目已顺利完成科技部验收。公司此次承担“光外送粉激光熔覆系列喷头研发与集成”的课题,完成了激光深孔熔覆加工头、激光变焦熔覆头等9种光外激光熔覆头,其中已有6款通过装备系统集成提供给用户实际应用,解决了高功率连续工作工况应用。这些激光熔覆头将集成在激光熔覆设备上用于冶金、煤炭、机械、化工、军工等行业。
8. 激光3D打印
该工艺采用激光熔覆技术,使用激光照射喷嘴输送的粉末流,直接熔化单质或合金粉末,在激光束离开后,合金液体快速凝固,实现合金快速成型。目前,已在工业造型、机械制造、航空航天、军事、建筑、影视、家电、轻工、医学、考古、文化艺术、雕刻、首饰等领域获得广泛应用。
激光表面处理及再制造典型行业应用
当前,激光表面处理及增材制造技术、工艺和装备被广泛应用于冶金、矿山机械、模具、石油电力、五金工具、轨交、航空航天、机械等行业。
激光表面处理及再制造的常见应用领域
1. 冶金行业典型应用
例如,针对42CrMo钢材的轧机驱动齿轮轴激光熔覆工艺,硬度可从HRC 22-25提升到HRC 35-42;熔覆层的单边为1.2mm。工艺特点表现为轴承位修复、恢复成品尺寸、耐磨性能大幅提高。另外,针对铸钢的轧机牌坊激光修复,加工后可从日常磨损的凹槽、腐蚀坑转变为机架尺寸的恢复如初,修复后使用寿命可提高2倍。
轧机驱动齿轮轴激光熔覆
又如,对T2材质的铜喷嘴进行激光熔覆后,能够对易受损的基材(铜)的使用寿命提高1-2倍。工艺流程耐高温、耐麿涂层、无开裂、无气孔,可实现废品利旧,循环再用。
铜喷嘴激光熔覆
2. 煤机行业典型应用
针对27 SiMn钢材的液压缸激光熔覆,替代了传统的电镀工艺,加工后硬度为HRC50-60;熔覆单层0.6-1.5mm,基材的耐磨、耐腐蚀性能显著提升。
3. 模具行业典型应用
针对中碳钢的模具激光淬火,硬度从 HRC22-25增加到HRC55-58;淬火层厚度为0.6-1.2mm;工艺特点显示为局部硬化、不变形、边角未出现烧融塌边现象,有效替代传统热处理无法处理的成型模R角选区淬火手段。
中碳钢的模具激光淬火
4. 轨道交通行业典型应用
无论是车轮和钢轨激光除锈、车身焊缝处理和钢轨除氧化层,激光清洗技术都可以具备基材无变形、绿色环保高效以及操作便捷无耗材等特点。
5. 航空航天行业典型应用
钛、铝、合金系列的航天零件和原材料的激光清洗工艺处理,采用50-2000W功率的设备,清洗效率为0.5-8m2/h;精细高效,基材无损伤,有效替代传统的手工打磨和化学清洗等工艺。
钛板激光清洗
发动机过滤网激光清洗
其它行业应用领域
未来发展与创新
据统计,中国平均每年都会由于关键基础零部件失效造成巨大的工业损失(约占国民经济总产值的3%-5%)。其中,80%以上是因表面局部磨损、腐蚀等失效引起的,直接损失超过万亿元。鉴于此,这推动了加工精度高、易于数字化控制、效率更高的激光增材制造和表面处理技术进一步发展与普及,该技术已被证明在机械制造与维修、冶金、煤矿、汽车、航空航天和石油化工等领域中有广泛的应用空间。
随着中国智能制造的持续发展与革新,加工对象、工艺方法、应用领域等,随之不断拓展。近年来,中国仅在高端清洁领域如航空航天、轨道交通、汽车制造等工业清洗市场就达上千亿元。国内金属3D打印技术的不断完善,补充了传统工艺的开模难、精度低,耗时久、组装繁琐等弊端,对高端装备制造推波助澜。激光表面处理技术在模具、五金工具等行业,使低等级材料实现高性能表面改性,实现零件制造低成本、寿命长,具有非常可观的社会与经济效益。
诚然,激光表面处理及增材制造领域也在创新上面临了不少挑战,关键是要实现新旧工艺和理念上的转换。材料方面,亟需攻克新材料研发;新类型材料的批量化及材料成本问题。装备上看,攻关方向包括光源的稳定性;镜片功率的承载;光路配置的优化;智能控制技术;和装备的小型化等。同时,针对工艺层面,要继续加强对激光工艺的极限探索;复合工艺的深入挖掘,使技术能够适应和契合更多行业的工艺需求。
展望未来,激光表面处理及增材制造设备发展方向可归纳为以下几点:高效率——加工效率高,满足现代工业快速生产节奏;高性能——设备功能多样化,性能稳定,适用不同工况;高智能——智能化水平不断提升,人工干预少;低成本——设备成本可控,耗材成本降低;定制化——设备个性化定制,精准售后服务,以及复合化——激光技术与传统加工技术相结合。