-
新闻资讯
- 激光应用
- 行业资讯
- 久恒风采
销售热线:17758118083
电话:0577-66871553
邮箱:sale@highlaser.cn
1688网店:https://laser2015.1688.com
总公司地址:浙江省瑞安市阁巷新区东二路138号32幢
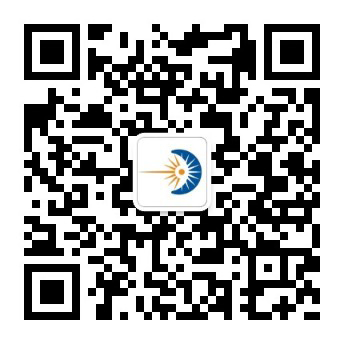
对于钢结构件的激光表面硬化处理,以往采用二氧化碳激光器系统能耗大,光电转换效率只有10%,因此没有流行起来。如今,随着高功率半导体激光器的发展,其光电转换效率提高到了50%,完全克服了这一缺点,且激光具有诸多优点,因此提供了一种经济有效的替代常规感应淬火硬化的方法。
热处理原理
热处理是一种提高钢件耐磨性和抗疲劳性的常用方法。在这一过程中,热源靠近工件表面,将指定区域加热到900 ~ 1500℃,钢件中的铁素体转变为奥氏体。此时,碳原子沉积在高温晶格结构中。随后冷却到100°C以下,由于冷却速度快,碳原子不再向外扩散,结果形成了硬质马氏体。
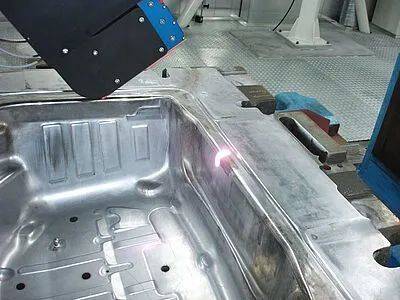
图1 对模具表面进行激光硬化处理
感应淬火硬化处理
感应淬火是一种常用的热处理方法。其原理:零件通常放在一个铜线圈内,线圈内通过一定频率的交流电。线圈和零件组成一个振荡电路。这一过程导致高频磁化,然后引起工件加热。磁场耦合很大程度上取决于零件几何形状,而且加热会发生在不应该加热,或者不应该加热那么多的区域。当感应淬火对零件局部输入过高能量时,会导致材料变形。对于一些非常精细的结构,这只能通过额外的后处理工序进行纠正。此外,感应淬火件必须通过浸入淬火液来冷却。水基淬火液的循环和冷却要花费额外的能量。
感应淬火过程如此麻烦,为什么仍然经常被作为首选工艺呢?因为相比较激光表面硬化处理,感应淬火更加经济。以往采用高功率二氧化碳激光器,电光转换效率只有10%,钢表面吸收光能效率最大40%(在不使用吸收增加涂层条件下)。这种类型的激光实际上只能提供不足4%的能量转化效率,并且价格昂贵。
而感应淬火硬化过程能量转化效率在15%-63%之间,实际值取决于零件的形状。即使把后处理工序和淬火液循环冷却的成本计算进去,感应淬火总成本还是低于激光系统的投入和操作成本。因此,这就容易理解为什么如今许多用户还是喜欢感应淬火工艺。
大功率半导体激光器
然而,以上观点并不能反映当前激光技术的发展。特别是如今高功率半导体激光器,其光电效率可达50%以上,明显优于二氧化碳激光器。这大大降低了能源消耗。另外,市场上半导体激光器的流行,也促使了其采购成本的降低。
对于相同的零件,基于半导体激光器的表面热处理,只需要消耗感应淬火过程10%的能量。一个主要原因,对于几何外形复杂的零件,外部线圈加热效率较低,能量消耗大。例如,对于凸轮装置,需要对几处连接关节的接触表面进行硬化处理。由于其形状独特复杂,无法采用感应淬火处理。这种情况下,激光系统有一个非常明显的优势:激光束聚焦且精确定位,可进行选择性处理,仅对选定区域进行表面热处理。同时,与光学温度监测系统组合后,如热摄像头和高温计,可对加热温度进行定量调节,避免温度过低或者局部过热。
由于快速加热,选择性加工和精确的温度控制,每束激光的热量在最短的时间内消散,不需要另外的淬火冷却液。几乎没有材料变形,不需要后处理矫正。整个过程明显减少了时间和成本。
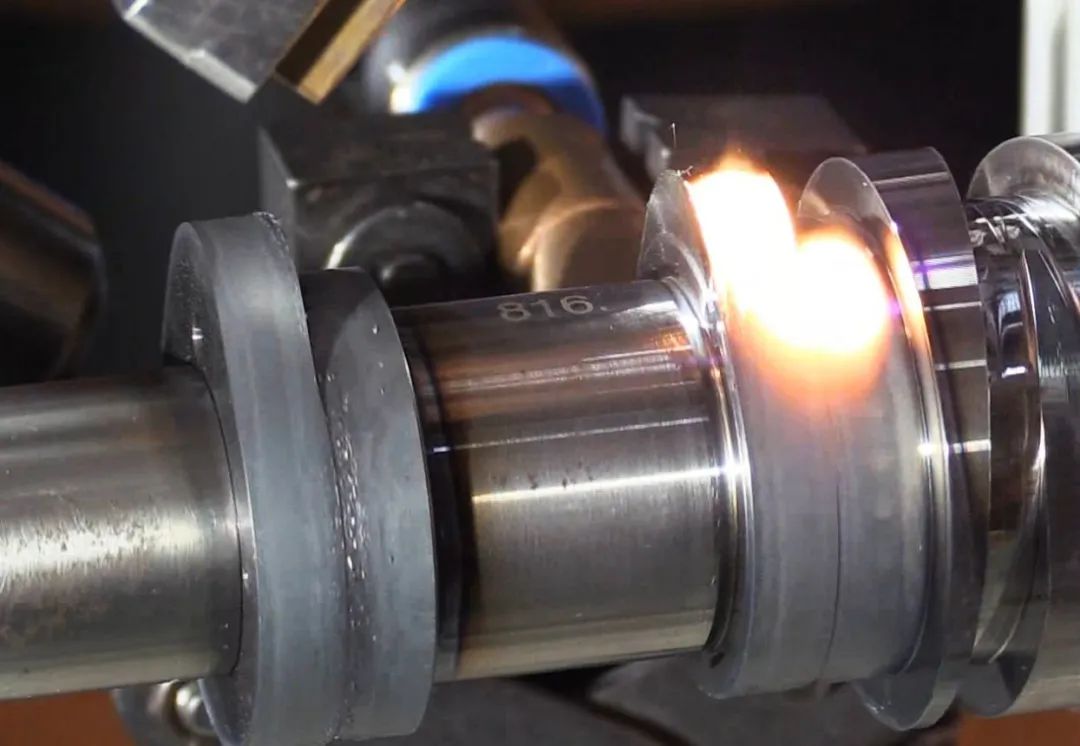
图2 激光零件表面硬化处理
图3 凸轮接触表面热处理
采用半导体激光器进行表面硬化处理,在经济上和在技术上都证明了其优势。半导体激光辐射,可以得到均匀的光强分布。可对平面进行均匀稳定的加热。另一方面,可通过透镜系统或者扫描镜头,对指定轨迹进行加热,并且可单独调整每个位置的加热温度。不管是小型零件到大型模具,都可以采用半导体激光器进行表面硬化处理
结论
激光表面硬化处理,始终优于感应淬火硬化吗?答案是NO。要根据实际情况进行选择,例如对于几何简单或者圆柱形状的表面,选择感应硬化更为明智;对于具有复杂几何外形的零件,要对选定的局部位置进行硬化处理,那么半导体激光器系统更为有效。在这种情况下,半导体激光器在能源效率方面远远高于感应硬化的方法。